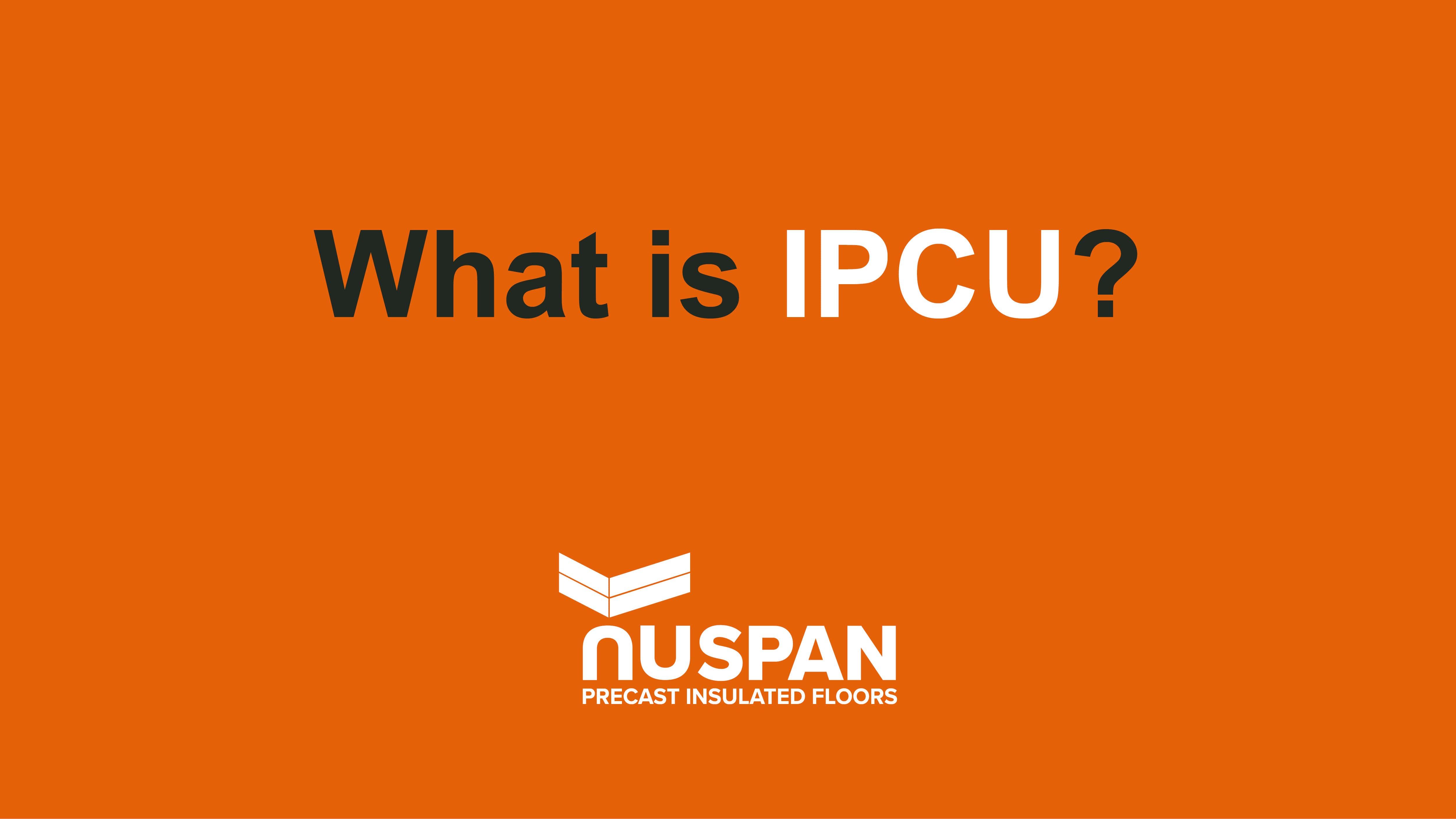
What is IPCU?
Insulated Precast Concrete Units (IPCU) are structural insulated closed floor panels combining structural-grade concrete bonded to high-performance expanded polystyrene (EPS). These slabs are used as an alternative to block and beam for the construction of suspended ground floors.
While traditional construction methods install the different materials separately, each IPCU slab contains concrete, steel for reinforcement, and the EPS, thus forming a continuous layer of insulation across the floor.
IPCU floors are usually manufactured offsite at the manufacturer’s factory, before being transported to site just in time for installation. As a result, the fitting process is significantly more efficient than traditional methods, partly because there is no need for storage or manual handling on site before installation, and partly because of the time which is saved from installing the concrete and insulation separately.
Why should we specify IPCU floors?
One of the major benefits of IPCU floors over traditional construction methods is the thermal performance which can be achieved.
The structural-grade concrete is poured directly onto the EPS and steel rebars, so the materials are bonded together. This avoids air gaps and minimizes heat loss brought about by air movement.
In addition, IPCU floors are designed to reduce heat loss at the junctions between walls and floors – areas that are usually responsible for a significant amount of a home’s heat loss. IPCU systems minimise this problem by bearing directly onto the inner leaf cavity walls, so the insulation extends beyond the floor to the face of the wall cavity. The insulation within the cavity butts up against the insulation in IPCU slabs, providing continuous insulation across the junction.
As a result, an IPCU floor is a thermally efficient construction method. With this system, it’s possible to achieve thermal U-values as low as 0.10W/m2K, allowing you to meet your Future Homes Standard Part L obligations already – years before the new building regulations become compulsory.
As well as helping the construction industry to meet corporate and environmental responsibility targets, this has a positive impact for future homeowners, in that the amount of fuel required to heat buildings using IPCU floors is reduced. The result is lower CO2 emissions and an improved whole-life carbon footprint when compared to traditional methods.
However, superior thermal performance is not the only advantage to IPCU floors. As a Modern Method of Construction (MMC), some of the other major benefits of IPCU floors are improved time, cost and material efficiencies. These all contribute to housebuilders meeting ambitious build programmes and industry targets, including the government’s aim to build 300,000 homes per year.
Nuspan Flooring’s IPCU system
Nuspan’s IPCU floor slabs can achieve clear spans up to 7 metres in length. Consistent thermal performance is achieved across this entire surface because the insulation runs continuously across the floor.
Each unit is made to measure, so where two units are placed next to each other, they can be butted up closely with the insulation layers sitting tightly together. There are no wide gaps between units – as is the case with other methodologies – which achieves a significant reduction in thermal bridging.
Nuspan’s NSAI-approved technical team can provide thermal calculations for each project, depending on customer requirements. The thermal performance is assessed in accordance with EN ISO 13370:1998 to ensure compliance with building regulations.
These slabs are made with Design for Manufacture and Assembly (DfMA) principles in mind. They are produced entirely offsite at Nuspan’s factory, and are delivered to site ready for installation.
Experienced installation teams can fit Nuspan’s precast flooring as quickly as one plot per hour. Not only is this around 500% faster than traditional construction methods – it also provides a reduction in labour of up to 83%.
Improvements of this magnitude have a significant impact on productivity and efficiency. As such, housebuilders can expect a higher Pre-Manufactured Value (PMV) percentage on projects specifying Nuspan’s precast flooring than those using traditional construction methods.
Read more about the benefits of using Nuspan precast flooring or contact us to find out more.
Tags: News