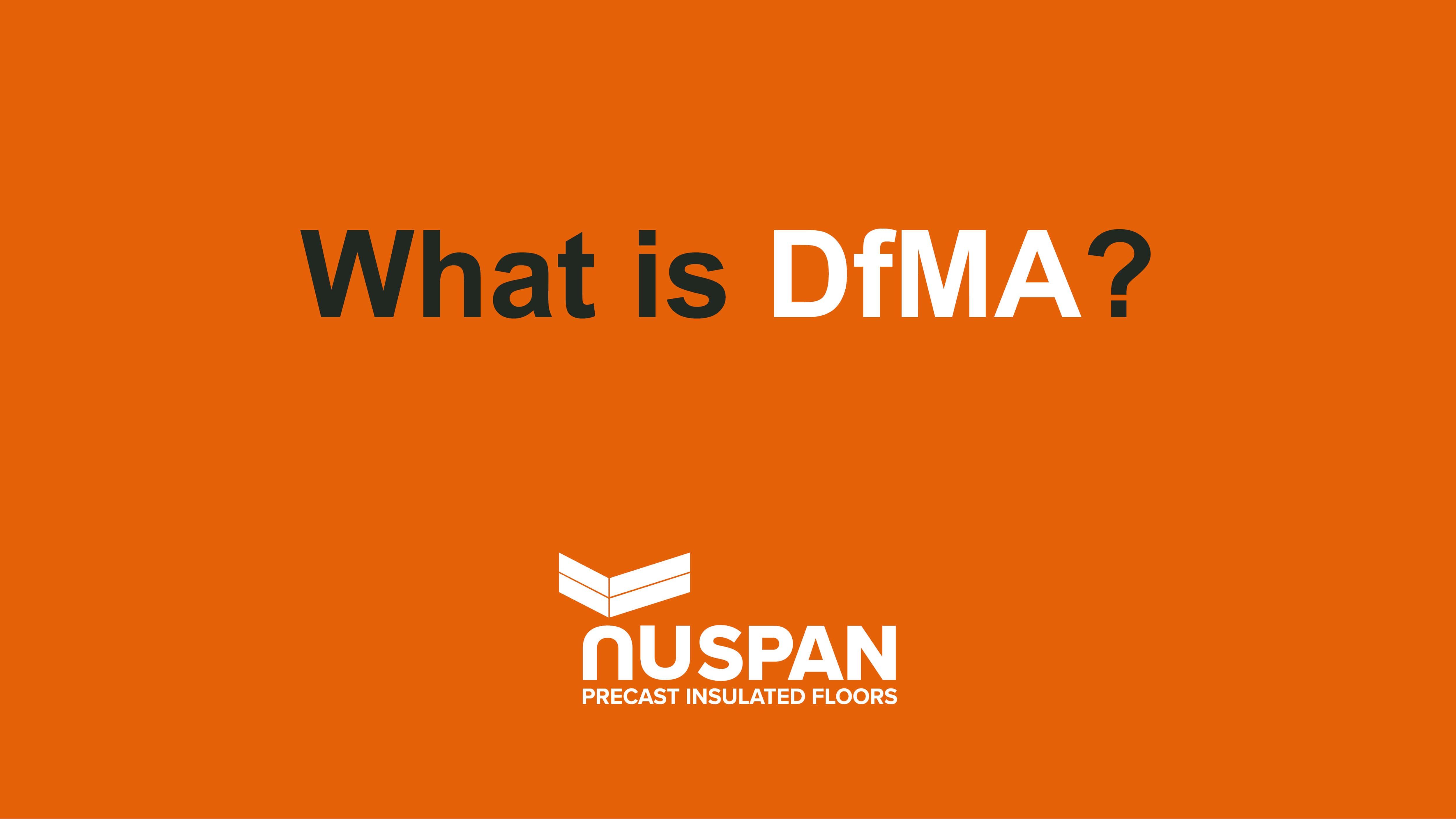
What is DfMA?
Design for Manufacture and Assembly (DfMA) is a combined term for two methodologies: Design for Manufacture (DFM) and Design for Assembly (DFA).
DFM focuses on simplifying the manufacture process without compromising on quality standards, while DFA ensures that installation on construction sites happens as quickly and smoothly as possible.
Both processes take place at the design stage, using various digital design tools including Building Information Management (BIM) systems. Perfecting the building products and installation processes at this early stage allows for consistent, fast and high quality production and construction.
Why is DfMA important?
DfMA is all about efficiency.
By designing for manufacture, designers are forced to look for the best and most cost-efficient materials for the application. They also consider the manufacturing process itself, to monitor and maintain quality, minimise disruption and increase operational efficiency.
This doesn’t just have benefits for the manufacturer. Choosing efficiency and quality at the production stage means that the costs for groundworkers and housebuilders are minimised.
Designing for assembly is similar in that designers aim to come up with products which can be constructed on site as quickly, easily and efficiently as possible. This could include factors such as the number of steps required for construction (or how complex they are), or even the number of components which need to be installed. In general, more individual components would take longer to fix in place, so by reducing the number of parts, there should be a knock-on reduction in terms of time and labour required.
It is important to take these considerations into account as early in the process as possible – particularly during the design stage – because it is significantly easier and cheaper to make changes to the design, materials or manufacturing process before manufacture has actually begun. If this does not happen, it is costly, time-consuming and frustrating to have to correct problems if they only arise once the products arrive on site.
Using DfMA with Nuspan Flooring
Nuspan’s precast insulated flooring is designed with DfMA principles in mind. The result is a system which combines three materials (structural-grade concrete, steel for reinforcement, and high-performance expanded polystyrene called EPS) into each unit.
This means that experienced installation teams can fit Nuspan’s precast flooring as quickly as one plot per hour, which is around 500% faster than traditional suspended ground floors where the concrete and insulation are installed separately.
In addition, the units are delivered with service openings already moulded into the slabs, so there is no need for cutting on site. As well as eliminating waste, this saves time and provides safe and quiet onsite working environments.
Nuspan uses DfMA to manufacture slabs to the requirements of the superstructures, not just the substructures. This is because they’re designed ready for the installation of other products on site, such as incorporating cantilevers or bolt fixings for other Modern Methods of Construction (MMCs).
This fast and efficient construction – which originates in DfMA – leads to a reduction in labour of up to 83%, reducing pressure on sites which have been experiencing labour and skills shortages.
Nuspan’s slabs are produced entirely offsite at Nuspan’s factory, and are delivered to site ready for installation. The high standards of productivity and efficiency make this system an MMC, as outlined by the MHCLG’s Definition Framework. As such, housebuilders can expect a higher PMV percentage on projects specifying Nuspan’s insulated precast concrete units (IPCU) than those using traditional construction methods.
Read more about the benefits of using Nuspan precast flooring or contact us to find out more.
Tags: News